Overcoming the limitations of conventional ultrasound sensors in NDT with proprietary and novel thin-film technology
14/04/2020
Ultrasound sensors are widely used to image internal defects in objects for non-destructive testing (NDT) and structural integrity monitoring, as well as in medical applications. Due to their non-invasiveness, high accuracy, extreme sensitivity and powerful penetration capabilities, ultrasound sensors are considered to be an increasingly powerful tool for NDT and other modern-day applications.Traditionally, ultrasound sensors tend to be manufactured using piezocomposite, piezoceramic or single-crystal materials, a process that has, despite incremental improvements, remained largely unchanged for over 40 years. There are, however, several limitations associated with conventional ultrasound sensors that can be attributed to the rigid and brittle nature of the ceramic-based materials used in manufacturing. These include poor connection to curved surfaces due to rigid construction, reduced performance at elevated temperatures and limited resolution for imaging and measurement.
Utilising the latest thin-film deposition methods, Novosound has created a novel and ground-breaking technique for the mass production of printable ultrasound sensors. This patented technology was developed at the Institute of Thin Films, Sensors and Imaging (ITFSI) at the University of the West of Scotland, where Novosound emerged as the university’s first ever spin-out company. Today, Novosound has grown rapidly to become a global business working across a wide range of diverse industry sectors and has received a number of awards from several leading institutions for its innovative ultrasound technology.
Novosound’s new type of ultrasound sensor is flexible, extreme temperature resistant, lightweight, low profile, compact and capable of producing high-resolution images. Overcoming one of the biggest challenges in NDT, Novosound’s flexible phased ultrasound array enables the inspection of curved surfaces and complex geometries in aerospace, automotive and industrial applications, whilst its ‘fit and forget’ ultrasound sensors provide asset integrity monitoring at extreme temperatures, significantly reducing downtime and saving costs. Designed for scanning acoustic microscopy and industrial inspection applications, Novosound’s High Resolution Immersion Probe allows for the detection of defects in small objects, delivering excellent acoustic and imaging performance.
Unlike machining and other manual processes used to make conventional ultrasound sensors and transducers, thin-film sensor production is an additive process capable of coating large areas of substrate for assembly into multiple devices. In thin-film manufacturing, a proprietary piezoelectric thin-film material is used to produce single-element and array transducers in batches, increasing probe-to-probe consistency. With considerable investment, Novosound’s in-house design and end-to-end manufacturing capabilities allow for the production of highly customisable and scalable ultrasound solutions that meet the most versatile inspection needs for a variety of modern-day applications.
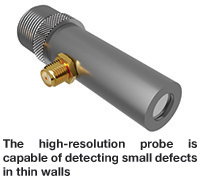
Capable of continuous operation at temperatures up to 400°C, Novosound’s Permanently Installed Ultrasound Sensor allows cracks and corrosion to be detected in pipes without the shutdown or cooling of assets, therefore greatly reducing costs and downtime for inspection. Pipe wall thickness monitoring is a crucial inspection method for the oil & gas industry and pipes carrying fluids up to 400°C must be regularly monitored for internal corrosion or erosion to prevent failure and allow for timely and targeted maintenance. The conventional piezoelectric materials used in ultrasonic sensors lose efficiency and acoustic output when exposed to increased temperatures due to their Curie temperature, limiting their effectiveness for continuous monitoring at standard operating temperatures.
In contrast, Novosound’s thin-film material is inherently piezoelectric and, not being a ceramic, does not exhibit a Curie temperature, making it an ideal material for high-temperature measurements. Novosound’s permanently installed sensors have been trialled continuously at 400°C for prolonged periods, reporting no loss of signal, and have also undergone initial thermal shock testing and outdoor trials, proving resilient to water ingress.
In addition, the highly flexible nature of the thin-film material allows sensors to conform to any pipe face, resulting in greatly improved measurements on challenging geometries with one model of probe. Coupling material stability is a significant issue at elevated temperatures and this conformability is advantageous because it permits coupling without the need for a gel- or oil-based couplant, which evaporate at high temperatures.
Furthermore, the additive process of thin-film manufacturing makes sensor production highly scalable and therefore makes the monitoring of large assets viable. This would not only remove the need for system shutdown for access, it would also remove the need for direct operator access to hazardous high-temperature areas. Novosound’s permanently installed ‘fit-and-forget’ ultrasound sensors can provide ongoing real-time data from narrow-diameter pipes and vessels, complex curves and geometries, and are operational at high temperatures. Monitoring real-time sensor output via a wireless cloud-based system can offer insights into equipment failure, from the degradation of materials to a part replacement, enabling a more responsive and agile production process.
Recently, an increase in computer-generated geometrical structures has led to the proliferation of more complex and contoured surfaces in aerospace. Generally, aircraft are designed for aeronautical efficiency rather than inspection.
Current phased array ultrasonic testing (PAUT) transducers are typically constructed from a single piece of brittle piezoelectric ceramic or piezocomposite, which is then machined into multiple individual elements and wired to form a sensor array. Due to the rigid properties of the ceramic material, solid interfacial contact and inspection of tightly curved surfaces, such as turbine blades and composite parts, is challenging and leads to prolonged and costly maintenance, repair and overhaul (MRO) periods.
By exploiting the truly flexible nature of the thin-film material, Novosound has been able to develop a fully flexible ultrasonic array that can easily conform to complex geometries and tackle certain hard-to-reach areas where existing UT arrays struggle. At just 0.25 mm thick, Novosound’s low-profile flexible phased array enables the accurate ultrasonic imaging and inspection of complex geometries in aerospace applications.
Unlike rigid sensors, Novosound’s flexible array can be swept across the surface continuously without the need to stitch images together, whilst a wedge is no longer required for defracting angles. By simplifying the inspection process and reducing maintenance times, aircraft are able to spend less time on the ground and more time in the air, therefore saving significant costs.
For easy integration, Novosound’s technology is designed to be hardware agnostic and has been demonstrated to work with standard hardware (such as Sonatest’s VEO+ and Eddyfi’s Mantis) for NDT. The phased array itself can be customised to suit the most rigorous requirements, including changes to dimensions, curvatures and configurations (linear, 1.5D and matrix).
With the propagation of computer-generated complex geometries and the implementation of increasingly sophisticated data-exchanging industrial systems, the NDT industry is challenged to keep up with ever-evolving technological shifts and demands. Representing a cost-effective and scalable alternative to conventional ceramic-based ultrasound manufacturing, Novosound’s proprietary and ground-breaking thin-film material provides enhanced durability, hardware compatibility and flexibility to overcome many of the existing limitations faced in NDT. Moreover, the additive process of thin-film manufacturing allows for the production of multiple devices for highly scalable asset coverage, enabling an interoperable framework of ultrasound sensors for continuous asset monitoring and predictive maintenance.
www.novosound.net