Carrying out NDT and CM
Why is NDT carried out?

It may be necessary to ensure that a manufactured component meets a design specification. For example, a ball bearing must be of the correct size, perfectly round, with a good finish, correctly hardened and, most importantly, be free from defects.
All these parameters can be checked by non-destructive testing.
How is NDT carried out?
Many inspection and examination techniques are available, each with its own particular capabilities and limitations:
Visual examination
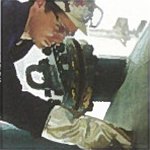
Liquid penetrant testing
This is probably the most widely used NDT method. It is a simple, low-cost technique for detecting surface-breaking flaws. The test object is coated with a visible or fluorescent dye and any surface-breaking imperfection draws in the penetrant by capillary action. After cleaning away excess penetrant from the surface, a developer is used to act like blotting paper to draw the penetrant from the imperfection, thus revealing the defect. This method is widely used in the aerospace industry for the detection of defects in light metal alloys.
Magnetic particle testing
In MPI, a magnetic field is induced into the surface of a ferromagnetic material. Surface imperfections result in local distortions of the magnetic field and magnetic particles sprinkled on the surface are attracted to these distortions, revealing the presence of surface defects. This method is widely used in the iron and steel sectors on all types of components.
Radiography
Radiography uses X or gamma radiation to produce an image of an object on a film. The principle being used here is the differential absorption of radiation by the materials being tested. For example, a piece of metal containing a gas pore absorbs less radiation than sound material. Thus, a piece of film placed behind the sample is more darkened behind the pore than elsewhere so that the gas pore is revealed in the developed film. Metal castings are commonly examined by radiography for internal defects in much the same way that medical radiographs are used to show broken bones.
Ultrasonics
Ultrasonic testing uses high-frequency sound waves to detect defects in solid materials. The most commonly used technique is pulse echo, where sound is introduced into the test object and reflections are returned to the receiver from internal imperfections of the geometrical surfaces. The principle is similar to the sonar devices used at sea.
Welds in nuclear reactors and pressure vessels are examined by ultrasonics. Ultrasonic methods are also used for the investigation of the materials which constitute the human body and about a quarter of all medical imaging studies worldwide are ultrasound studies.
Eddy current
In eddy current inspection an alternating current is passed through a coil and this causes an eddy current to flow in the material under test. If the coil is moved near a surface crack, a difference of eddy current is detected, which reveals the crack and can indicate the depth of the crack. Aircraft wheels are examined by this method. Eddy currents can also be used to detect changes in material conductivity and in component dimensions.
This method is widely used in automated inspection plants typically for automobile steering and brake components.
Condition monitoring
Another area of NDT is known as condition monitoring. Manufacturing equipment wears and may ultimately fail. Costly breakdowns can be avoided by using vibration monitoring techniques on bearings to indicate alignment problems, for example. The analysis of metal particles from gearboxes gives early warning of impending failure and can therefore help with preventive maintenance.
Other methods
NDT is a continuously developing area of technology and, in addition to the above widely used methods, other techniques such as acoustic emission, which 'listens' to the growth of a crack, leak testing and thermography all have an important part to play.
For more detailed descriptions of the various NDT methods, click here.
For more detailed descriptions of the various methods of CM, click here.
