Glossary of Terms
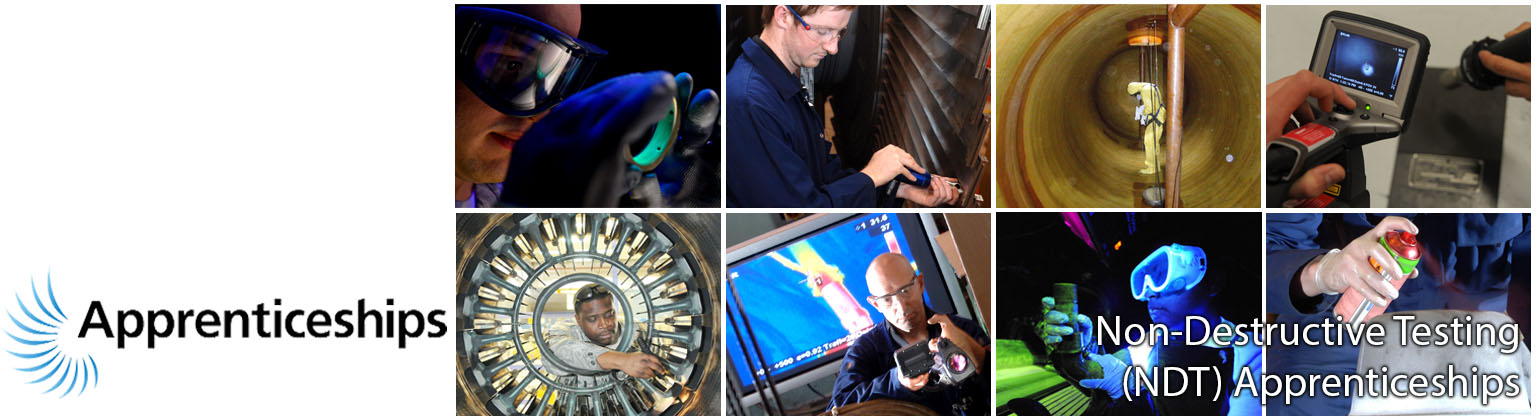
Relevant mathematics, including numerical and data analysis, that is necessary to support the application of technical and practical skills – NDT relies on understanding aspects of mathematics so that equipment can be set up properly. All results from NDT equipment need to be interpreted and this can be in the form of numerical readouts, graphs, images and spreadsheets. Some areas of mathematics, such as trigonometry, are critical for locating defects, while statistics can be used as an aid to compile and analyse results.
Formula-based engineering and the scientific principles underpinning relevant current technologies – NDT relies upon the ability to use mathematical formulae to work out the correct settings for equipment. The most common formulae used are trigonometric and equations will need to be solved to obtain the correct inputs and outputs from the instruments. These aspects are taught on the NDT training courses, which explain the background physics, electronics and material properties knowledge needed to understand the inputs and outputs for the equipment.
How to use materials, equipment, tools, processes and products relating to NDT – NDT usually involves bringing together a collection of various components, including equipment, probes, media and the item or product under inspection, in a particular configuration that optimises the potential for the detection of unwanted flaws, features or characteristics in the latter. The detailed steps in configuring such a test system and applying the test to products of a specific size and shape is usually provided in the form of a written work instruction.
Preparation of NDT procedures, technique sheets and work instructions for use by NDT operators – In order to detect relevant discontinuities within a material or component with a high degree of confidence, NDT methods need to be applied in a standard, repeatable and controlled manner. Often, the test method will also have been validated to demonstrate capability in detecting relevant discontinuities. Based upon international standards, codes and working practices, NDT procedures, technique sheets (TS) and work instructions (WI) capture these requirements, describing how an organisation controls and undertakes its specific NDT inspection activities, both from a quality management system perspective (procedures) and in giving clear and concise instructions for NDT operators to perform inspections (TSs and WIs).
How to use and apply information from technical literature, codes of practice and industry standards – There is a great amount of information available relating to inspection by NDT methods. The standards will call for the inspection of the item by the NDT method(s) and there are relevant British, European and international standards relating to the use of the NDT method from which the appointed Level 3 will have written a company procedure. There can also be task-specific instructions that either the Level 3 or a Level 2 will have written. The appointed Level 3 should be accessible to guide the Level 1 and Level 2 inspectors on the use of technical literature, codes of practice and industry standards and facilitate any necessary specific training if required.
The limitations of standard tests and measurements relevant to their field of activity – NDT usually involves bringing together a collection of various components, including equipment, probes, media and the item or product under inspection, in a particular configuration that optimises the potential for the detection of unwanted flaws, features or characteristics in the latter. The detailed steps in configuring such a test system and applying the test to products of a specific size and shape is usually provided in the form of a written work instruction.
Industry-specific product technology, including material types, defect types, defect mechanisms, growth rates, industry-specific NDT applications and R&D opportunities – How products are manufactured plays a fundamental role in how defects or anomalies can arise in them. Sometimes these will be perfectly acceptable features of the product and at other times you will need to reject the product. When you NDT a part, you should be able to understand how it is made so that you can anticipate where to look for relevant defects. Many potential defect types exist (surface and sub-surface) and these vary with how products are made. Research and development (R&D) plays a vital role in NDT as it can lead to increased efficiency through a reduction in cost, a reduced processing time or an increase in capability.
How to use the results of engineering NDT analysis for the purpose of developing solutions to well-defined engineering problems – Being able to set up NDT equipment accurately and interpret the results is important. Many factors can affect the results for both the input and output of any equipment. NDT is highly dependent on the properties of the materials being tested (density, conductivity, surface roughness, etc) and the environment in which NDT is being conducted (for example under water, inside a pipe, near a weld, on a painted product and so on).
The need to gather contextual information prior to the inspection required for the assessment of defects against acceptance/rejection criteria – It is important to know what the aim of the inspection is and to have a set of rules that inform the interested parties on what flaws will be assessed against, in terms of dimensions, characterisation and position. These requirements can be found in the relevant national, European and international standards, along with company-specific codes and standards. The organisation that has a requirement to have an item inspected must agree with other interested parties, such as design authorities, insurers, etc, on which of the standards are to be used. Before the inspection commences, the inspector will know which acceptance/rejection criteria is to be used and, as an example, it could state that no cracks are allowed or that porosity less than 10 x 10 mm is acceptable but any larger areas are rejected. This allows the inspector to accept/reject all flaws found.
Project management processes and key points – A project is a discrete piece of work that is designed to achieve a planned outcome. It has to be completed within an agreed budget, within a defined time and to a specified quality. This can only be achieved if the project is managed from start to finish. The various activities have to be planned and coordinated. The resources needed have to be made available at the required times and the project team needs to know what is expected of them and when. A project can only be managed if progress against the plan is measured and if any risks, such as a key input being delayed, are anticipated and corrective actions taken early. A project manager needs to have good communication with everyone involved in the project.
The consequences of failure and the risk to life and the environment – Many industries use components, materials and plant items, which, when operational, are subject to immense stresses and risk and therefore the likelihood of failure is high. To mitigate the risk when justifying continued operation, extensive NDT is carried out that helps to make the necessary operational safety case. The consequences of failure could result in loss of life, an adverse environmental impact and commercial penalties. Very often the results of NDT inspections are not rechecked and are taken at face value and therefore it is essential that the NDT results are correct and that the NDT operators, NDT engineering technicians and NDT engineers are fully aware of the importance and the impact of their role.
Ability to conduct re-inspection audits of NDT operators’ work, comparing and evaluating the results and taking appropriate action when necessary – Surveillance is performed in order to provide confidence that the inspection activities performed by NDT inspection personnel are true and accurate. It is often a requirement of the organisation’s specific Quality Management System (QMS) that re-inspection activities are carried out. Surveillance can take the form of operator/equipment/documentation reviews, re-inspection of the operator’s work, witnessing of inspections and dataset/radiograph/NDT report reviews. Where discrepancies or failures are identified, then corrective and preventative measures defined within the organisation’s QMS are formulated and actioned with a high degree of professional conduct to mitigate a further repeat of the issue.
The knowledge required for the assessment of defects against acceptance/rejection criteria – Have an understanding of the flaws likely to occur in the product form tested, together with the way they are indicated with the test method used. Have the ability to interpret the acceptance and/or rejection criteria and have the skills needed to measure any flaw indicated and to accurately assess it against that standard. Understand the uncertainties inherent in the tests and measurements carried out and how they impact on the decisions made.
Exhibit environmental awareness and undertake safe working practices for self and others – Be aware of the potential impact of your actions or inactions on the natural environment and demonstrate awareness by avoiding possible damage. Be able to consistently recognise risks to your own and other people’s and health and safety and take active steps to reduce them. Recognise improvements that can be made and communicate them to the appropriate department.
Demonstrate a disciplined approach relating to industry standard operations and processes – Strict adherence to the procedures and work instructions that have been provided for use and that have been developed by the employer as compliant with the relevant appropriate national and international standards.
Validation of NDT processes – Validation produces evidence to show that an inspection will achieve the detection of the defects that need to be found. It can also check that the defects found are able to be sized to the required accuracy. It can be achieved by the systematic introduction of known defective products having features or flaws of a predetermined size or severity commensurate with the end-user’s specified limits, prior to, during and on completion of the NDT inspection of batches of identical products, or designated areas or volumes on very large products, such that consistent detection of flaws to the required standard is verified at intervals throughout the inspection and not simply assumed from an initial check or set-up.
Material properties, electronic principles, mathematics and technical project management – The characteristics of the material from which an item under inspection has been manufactured or constructed dictate how the item will perform in an intended application or environment. Strength, hardness, toughness, ductility, abrasion resistance and corrosion resistance are some key properties in this context. In the context of the performance of NDT, more basic physical properties, such as electrical conductivity, permeability and density, are considered in the selection of an appropriate test method.
Commercial awareness and the economics of their industry sector, business improvement and project and business management techniques relevant to the engineering industry – The understanding that the planning, preparation, execution and reporting of NDT tests invariably incur costs that must be reasonably limited and controlled such that those costs do not outweigh the sale value of the product itself or the perceived benefits, such as medium- or longer-term financial savings that result from effective ongoing asset protection and subsequent working life extension of parts and plant in service.
Regulatory and international standards requirements, technology, safety and the environment – Where the execution of NDT presents potential environmental impact or safety hazards, there are likely to be associated regulatory standards that mandate NDT procedures to address the specific issues or concerns contained therein, in a manner that mitigates the risk to the NDT inspector, local workforce, general public and the environment, to a recognised acceptable level.
Applying design processes, including materials selection, that meet NDT standards – A process that aims to produce a solution to a given inspection problem or requirement, by proper consideration of the product or materials to be inspected and specific inspection requirements. In the case of the former, their dimensions, shape, surface condition, properties, common flaw types and their likely composition, morphology, position and orientation are significant. For the latter, sensitivity, resolution, coverage, precision and inspection rate are prime considerations.
Root cause analysis and learning from experience (LFE) processes – A disciplined, exhaustive process, utilising established investigative tools, that strives to identify the true origin of, or reason for, a particular unwanted event or condition, such that a permanent and effective solution can be implemented in order to prevent recurrence.
The advantages of collaboration with other industry sectors in order to apply best practice – The sharing of ideas, information and experience in the application of particular NDT methods and techniques as applied across a range of industry sectors, their associated products, environments and specific inspection requirements, aiming to identify commonalities or best practice and potentially more universal adoption of those particular aspects, where possible and appropriate.
Have advanced skills in NDT methods substantiating their lead competency role within their organisation and industry sector. Work in all industry sectors, such as nuclear or aerospace – A level of skill above that normally found or expected of NDT practitioners such as operators or technicians, developed as a result of wider experience in the application of a particular NDT method, across a broader range of sectors, or to a greater depth as a result of further training or more prolonged engagement with equipment manufacturers, as necessary for an NDT engineer who will potentially provide longer-term in-situ support of a particular test system and its operators.
For further information contact:
The British Institute of Non-Destructive Testing, Midsummer House, Riverside Way, Bedford Road, Northampton NN1 5NX, UK.
Tel: +44 (0)1604 438300; Fax: +44 (0)1604 438301; Email: apprenticeships@bindt.org