Latest Branch News
News from the Institute Branches
| Scottish Branch
Annual Technical Seminar, Exhibition and Burns Supper
Fraser Hardie reports
The Scottish Branch’s Annual Technical Seminar, Exhibition and Burns Supper took place at the end of January at the Golden Jubilee Conference Hotel, situated in the post-industrial landscape of Clydebank. This area of Clydeside has a rich shipbuilding history, sadly much depleted, which spawned many local non-destructive testing (NDT) legends of yore.
Nevertheless, the NDT profession in Scotland remains buoyant and this was reflected in the excellent attendance at each of the events, with representation from both nearby and further afield.
The theme of the technical seminar was: ‘The role of NDT in the assessment of asset integrity’. Five technical presentations, demonstrating the importance of NDT in effective asset management, were delivered during the day by Iain McDowall (Altrad Babcock), Marc Whitton (Air Control Entech), Conor Douglas (BP), Paul Wilkinson (Wilkinson Coutts) and David Bell/Blair Forrest (EDF). The breadth of talks encompassed nuclear, conventional and renewable power scenarios, as well as oil & gas plant. A concluding Q&A panel session generated a lively debate. It seems that, despite the evolution of NDT 4.0 and artificial intelligence, reliable NDT applied and analysed by suitably qualified and experienced personnel (SQEP) remains an essential element of effective asset integrity management.
The exhibition, involving 13 companies, ran throughout the day, providing the focus for networking, catching up with the latest NDT equipment and renewing acquaintances.
In the evening, many of the participants reassembled for the Burns Supper, which included a number of traditional elements but with added dancing (ceilidh). Charles MacLeod was an excellent MC for the night, whipping through a busy programme with contributions from Mike Farley (Immortal Memory), Iain Baillie (Toast to the Lassies and Tam O’Shanter), Caroline Bull (Reply from the Lassies), Jimmy Fraser (Address to the Haggis), Des Nicholl (piper), Stephanie Bell/Calum Lowe (singers), Fraser Hardie (Selkirk Grace and Vote of Thanks) and the Elderberries (band).
A raffle, with prizes donated by Agility/ETher NDE, Argyll Ruane, BINDT, CAN, Inspection Connection, RSL and TPAC, raised a substantial sum for BINDT’s Benevolent Fund.
The culmination of the evening was the presentation of the Bob Service Award to a young person working in NDT in Scotland who has demonstrated excellence in their profession. The winner this year was Keir Loudon of Altrad Babcock. Iain Baillie, as a Past President of BINDT, stepped in for the current President to make the announcement and presentation of the award (named in memory of one of those local NDT legends).
The entertainment, quality fare, drink (not least) and convivial company all contributed to a great night.
The successful organisation and running of the events depended on strong support from Karen Cambridge and her team at BINDT headquarters.
Annual Technical Seminar, Exhibition and Burns Supper
Fraser Hardie reports
The Scottish Branch’s Annual Technical Seminar, Exhibition and Burns Supper took place at the end of January at the Golden Jubilee Conference Hotel, situated in the post-industrial landscape of Clydebank. This area of Clydeside has a rich shipbuilding history, sadly much depleted, which spawned many local non-destructive testing (NDT) legends of yore.
Nevertheless, the NDT profession in Scotland remains buoyant and this was reflected in the excellent attendance at each of the events, with representation from both nearby and further afield.
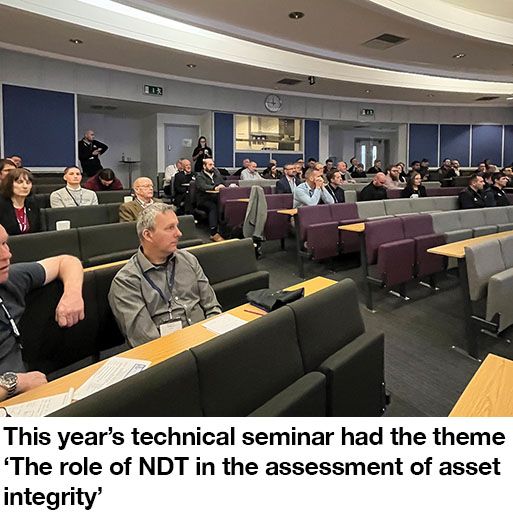
The exhibition, involving 13 companies, ran throughout the day, providing the focus for networking, catching up with the latest NDT equipment and renewing acquaintances.
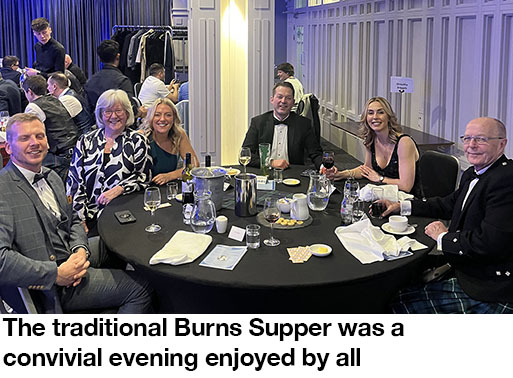
A raffle, with prizes donated by Agility/ETher NDE, Argyll Ruane, BINDT, CAN, Inspection Connection, RSL and TPAC, raised a substantial sum for BINDT’s Benevolent Fund.
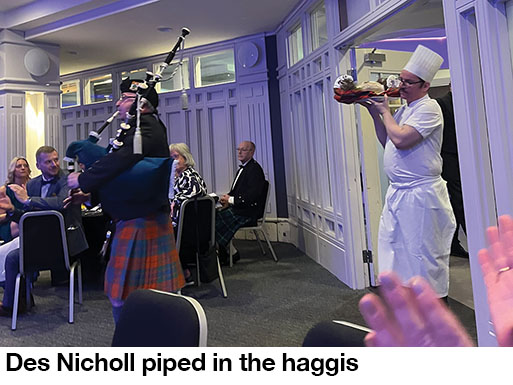
The entertainment, quality fare, drink (not least) and convivial company all contributed to a great night.
The successful organisation and running of the events depended on strong support from Karen Cambridge and her team at BINDT headquarters.