RBI
Risk Based Inspection
RBI – Risk Based Inspection is a method of deciding what component to inspect. In the past, each item of plant was generally inspected at set intervals of time, for instance every 12 or 24 months. By taking a Risk Based approach to planning inspections, the decision to perform an inspection and the inspection interval is selected based on the Risk of the plant item or component failing.
The Risk is assessed by asking two questions:
What would happen if the item failed?
The answer to this question is the Consequence of failure. In standard RBI analysis, it is then categorised in a range from Low to High. Often there are just three categories: high, medium or low. For instance, if a pipe carrying water fails, and the pipe leaks before it breaks, the consequence would be considered Low. However, if the failure of an item could result in an explosion or a release of toxic material then the consequence would be considered High.
How likely is it that it will fail?
The answer to this question establishes the Probability of failure, in other words the chances of failure actually happening. Again, in standard RBI analysis, the probability will be categorised in a similar manner to the consequence.
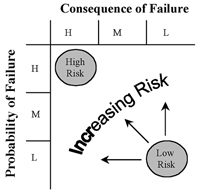
Having established the consequence and probability for each item in a plant, the results can be plotted on a diagram similar to that shown. Items with a High Consequence and a High Probability (top left of diagram) are considered High Risk. Likewise, items with a Low Consequence and a Low Probability (bottom right of diagram) are considered Low Risk.
Steps are then required to reduce the risk of the high risk items, ie move them down and to the right on the diagram. Such steps may include modification to the plant to reduce the consequence if the item did fail or changing the process conditions to reduce the chance of it failing.
The use of NDT is another way of reducing the risk but it can only do this by reducing the probability, by detection of damage before the item fails, ie it can only move the item down the diagram, it cannot alter the possible consequence.
The Risk Based approach has been used as a way of reducing the NDT bill by increasing the interval of the NDT applied to Low Risk items or removing it altogether. However, it does target NDT at the High Risk items, where it gives most benefit, and it has meant that the defects requiring detection have generally been identified so that operators should know what they are looking for. The results of any NDT performed under an RBI approach should be fed back into the Risk Assessment and changes made as appropriate.
For more information see:
HSE Contract Research Report: CRR 363/2001 Best practice for risk based inspection as a part of plant integrity management which can be downloaded from http://www.hse.gov.uk/research/crr_htm/2001/crr01363.htm
See also: HSL Report HSL/2002/20: Risk Based Inspection – A Case Study Evaluation of Onshore Process Plant which can be downloaded from http://www.hse.gov.uk/research/hsl_pdf/2002/hsl02-20.pdf
What the hec?! articles are not intended to be the definitive account on the topic or acronym in question. Readers’ comments and contributions are welcomed. Email: ndtnews@bindt.org
The Risk is assessed by asking two questions:
What would happen if the item failed?
The answer to this question is the Consequence of failure. In standard RBI analysis, it is then categorised in a range from Low to High. Often there are just three categories: high, medium or low. For instance, if a pipe carrying water fails, and the pipe leaks before it breaks, the consequence would be considered Low. However, if the failure of an item could result in an explosion or a release of toxic material then the consequence would be considered High.
How likely is it that it will fail?
The answer to this question establishes the Probability of failure, in other words the chances of failure actually happening. Again, in standard RBI analysis, the probability will be categorised in a similar manner to the consequence.
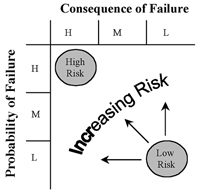
Having established the consequence and probability for each item in a plant, the results can be plotted on a diagram similar to that shown. Items with a High Consequence and a High Probability (top left of diagram) are considered High Risk. Likewise, items with a Low Consequence and a Low Probability (bottom right of diagram) are considered Low Risk.
Steps are then required to reduce the risk of the high risk items, ie move them down and to the right on the diagram. Such steps may include modification to the plant to reduce the consequence if the item did fail or changing the process conditions to reduce the chance of it failing.
The use of NDT is another way of reducing the risk but it can only do this by reducing the probability, by detection of damage before the item fails, ie it can only move the item down the diagram, it cannot alter the possible consequence.
The Risk Based approach has been used as a way of reducing the NDT bill by increasing the interval of the NDT applied to Low Risk items or removing it altogether. However, it does target NDT at the High Risk items, where it gives most benefit, and it has meant that the defects requiring detection have generally been identified so that operators should know what they are looking for. The results of any NDT performed under an RBI approach should be fed back into the Risk Assessment and changes made as appropriate.
For more information see:
HSE Contract Research Report: CRR 363/2001 Best practice for risk based inspection as a part of plant integrity management which can be downloaded from http://www.hse.gov.uk/research/crr_htm/2001/crr01363.htm
See also: HSL Report HSL/2002/20: Risk Based Inspection – A Case Study Evaluation of Onshore Process Plant which can be downloaded from http://www.hse.gov.uk/research/hsl_pdf/2002/hsl02-20.pdf
What the hec?! articles are not intended to be the definitive account on the topic or acronym in question. Readers’ comments and contributions are welcomed. Email: ndtnews@bindt.org