ECA
Engineering Critical Assessment
ECA – Engineering Critical Assessment – is the activity which is performed to decide the necessary actions to take once a defect in a component has been detected and sized by NDT. ECA is used to derive acceptance levels for flaws based on the concept of fitness for purpose, ie can the component be used for its intended purpose without reaching the conditions for failure within the time of operation? This is different to an acceptance level based on quality control of the manufacturing process.
ECA generates a failure assessment diagram by plotting the details of the defective component on a graph showing a fracture ratio Kr against a load ratio Sr. The assessment line divides the acceptable region from the unacceptable region. The Figure shows a Level 1 assessment diagram. Level 1 is a simplified assessment process. If this process shows the defect to be unacceptable, a more in-depth assessment can be performed which removes some of the simplifying assumptions.
ECA requires defect characterisation and size information from the NDT report and uses material properties, details of any operational and residual stresses and knowledge of the damage mechanism.
For more information on ultrasonic sizing and ECA see:
'Ultrasonic sizing errors and their implication for defect assessment', which can be downloaded from: http://www.hse.gov.uk/comah/sragtech/ndt4.pdf
For in-depth information on ECA see:
BS 7910:2013+A1:2015 Guide to methods for assessing the acceptability of flaws in metallic structures.
What the hec?! articles are not intended to be the definitive account on the topic or acronym in question. Readers’ comments and contributions are welcomed. Email: ndtnews@bindt.org
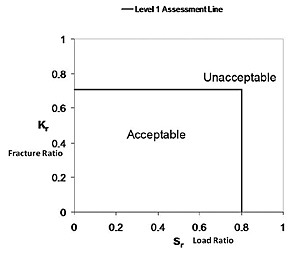
ECA requires defect characterisation and size information from the NDT report and uses material properties, details of any operational and residual stresses and knowledge of the damage mechanism.
For more information on ultrasonic sizing and ECA see:
'Ultrasonic sizing errors and their implication for defect assessment', which can be downloaded from: http://www.hse.gov.uk/comah/sragtech/ndt4.pdf
For in-depth information on ECA see:
BS 7910:2013+A1:2015 Guide to methods for assessing the acceptability of flaws in metallic structures.
What the hec?! articles are not intended to be the definitive account on the topic or acronym in question. Readers’ comments and contributions are welcomed. Email: ndtnews@bindt.org