Top ten questions to consider when selecting a measurement sensor
29/06/2021
Why do sensor suppliers ask detailed questions when it comes to solving a measurement task? With different measurement technologies and thousands of sensor variants to choose from, the answers to these questions help suppliers decide which sensor is best for the application. Glenn Wedgbrow, Business Development Manager at Micro-Epsilon UK, explains…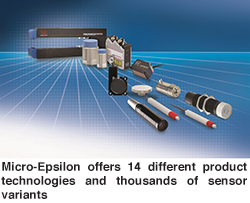
Here are the top ten questions to consider when enquiring about a sensor to solve a particular measurement task.
- What are you trying to measure? Can you describe the application? Do you have a drawing?
When contacting a supplier, it can often be difficult to imagine exactly what you want to do, especially over the phone. Pictures, drawings and photos can help the supplier to understand the requirements. - Why is it important to make this measurement? What is the benefit of acquiring the measurement?
Understanding the need of the measurement is crucial. It could be that the supplier ends up recommending a sensor or system over and above what was first imagined. However, if the implementation of a solution leads to the company saving thousands or tens of thousands of pounds per year, then it would be worth considering. - What are the technical requirements? How far can the target move, how fast does it travel and what tolerance needs to be achieved?
As a supplier, Micro-Epsilon sensors measure displacement (changes in position, thickness and so on) as well as measuring temperature and detecting/monitoring colour. Understanding the boundaries of the measurement helps to identify the possible sensor technologies. Tolerances are probably the most important information to provide to the supplier, as these ultimately define the real accuracy required in the application. - What is the target material and its surface condition?
If a supplier knows they are measuring against metals, plastic, glass, rubber or other materials, this will again help to define which sensor technologies could be used. It is also necessary to know if the surface appearance changes in terms of its colour, shine and temperature during the measurement task and if it is rough, smooth or varied, as this will also have an effect on measurement performance. - What is the shape, size and movement of the target?
This question is all about the physical aspects of the target. By understanding the geometry, a supplier can establish if the target is large enough for a specific sensor to be used, or if a small sensor spot size is required. - How much space is available to mount a sensor? What are the restrictions above, below and around the target?
This can often be overlooked but, if trying to fit a sensor into a small space (perhaps it is a retrofit or an upgrade), knowing how much room is available can often influence the type of sensor that can be used. Sometimes it might be possible to move the sensor further away from the target than first thought and look through apertures or windows. - What is the ambient environment for the sensor and the target?
These can often be different. By answering the above question, the supplier should now start to have a better idea of which sensor technology can be used; however, there may still be more than one option to consider. Make sure the location of both the sensor head and (if applicable) the controller are thought about. Key factors here will be the ambient temperature, cleanliness of the environment (for example dust, steam or oil), pressure or vacuum, as these can affect measurement performance and sensor accuracy. - What quantity is required? Is it a single measurement, multiple measurements on a single target required for multiple machines or a combination?
Left unanswered, this question could have serious implications on the success of the project. Having just one sensor to measure is easy to integrate. However, if measuring multiple positions at the same time, synchronisation and connectivity of the sensor(s) are important factors to consider. What output signal is needed is also important (for example analogue, digital, fieldbus). - Has a budget been defined for solving the measurement task?
The answer to question two can help to define a budget. However, if the required solution calls for more money than first thought, how can it still be justified? An incorrectly specified sensor chosen to meet a budget may just be money wasted if it does not measure as required. Before setting a budget, it can be beneficial to talk to the sensor supplier in order to help determine what a realistic budget should be. As a supplier, Micro-Epsilon will always aim to work to the defined budget, but if that results in a compromised sensor selection, it has to be considered whether this would be the best decision for the company in the long term. - When is a working solution needed by?
Most catalogue sensors are available from stock, but Micro-Epsilon also has the ability to customise parts of the sensor specification, for example by providing a non-standard measurement range, target-specific calibrations or different cable lengths. A bespoke sensor for original equipment manufacturer (OEM) requirements can also be created. However, these can take time and so it is best to talk to the supplier in plenty of time to help ensure the right solution is chosen, rather than one that ‘fits’ into a shorter timescale.