Gamma radiation control of brake disks for the rail industry
20/08/2009
IBRE was established in 2005 on the heritage of Pont-à-Mousson / Renk / SEE, the developers of the smart technology of cast iron friction rings moulded on (elastic) steel inserts. Today, IBRE develops and produces disk brakes and callipering systems in cast iron or steel, serving the rail industry, private networks and OEMs in France and the rest of the world.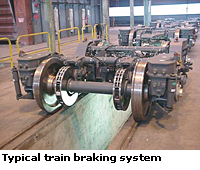
SGS Industrial Services has been in charge of brake disk testing for IBRE since 1988, carrying out gamma radiation control with Cobalt-60 for brake disks in accordance with European technical standards (for example NFE EN 12 681) and reference images ASTM E446 and E186. Cobalt-60 is a radioactive isotope of cobalt and is used in the industry to take images of welding seams and other structural elements for the detection of defects. SGS uses gamma rays as the casts are very large and weigh about 150 kilos each.
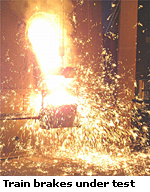
As the production of brake disks is on hold during the inspection period, it is very important that the SGS experts work very quickly. SGS radiation control is on the critical path of IBRE's supply chain, which is why it is essential that operations be processed without delay, and that experts are able to interpret the results quickly and reliably. Normally, the overall control process by SGS takes around 2 to 3.5 hours.
SGS not only identifies cast defects, but also deduces their causes. The usual causes for the defects are degassing issues, inappropriate temperature or incorrect speed of the flow. For IBRE, it is very important and helpful to pinpoint and understand what went wrong in the production process in order to fix the errors and prevent further problems.
Working for more than 20 years for IBRE shows that the company is very pleased with the work of SGS. Due to SGS's quick and reliable work, IBRE is able to maintain production quality. The support that SGS provides is particularly important in phases of change or process setting, where it can save days of production capacity.
SGS provides a fully integrated service pack for its clients, combining non-destructive testing services, inspection and asset integrity management through its worldwide NDT network in over 30 countries. The scope of SGS covers both conventional and advanced NDT methods, provided by qualified inspectors to international standards around the world.
www.sgs.com/industrial