Long-range ultrasonic testing reduces risk of unplanned shutdown
07/01/2010
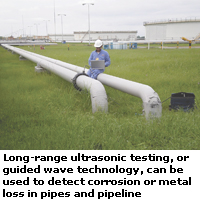
Similar problems occurred at the Chevron terminal in Escravos, Nigeria. Chevron, one of the world's largest energy companies, was having specific problems with risers due to corrosion and was subsequently looking for ways to inspect the risers without closing the whole field, which would have resulted in millions of dollars in lost revenue.
At this point, SGS offered to conduct long-range ultrasonic testing, which does not require removing clamps and can be applied for pipes in operation. Thanks to this relatively new inspection technique, Chevron was able to check the condition of the risers and schedule shutdown for repairs, thus saving costs.
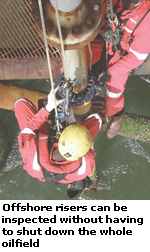
The guided wave technology screens 100% of the volume of the piping inspected. A typical application of LRUT is the detection of corrosion and metal loss in pipes and pipelines. LRUT uses guided ultrasonic waves which can travel many metres with minimal attenuation and therefore offer the potential of testing large areas from a single point using a pulse-echo transducer bracelet wrapped around the pipe.
This technology is particularly suitable for inspecting pipes in operation, insulated and even buried as the technique will supply the requisite data while minimising the need for removing the insulation along the piping.
Cost-effectiveness, safety and speed were decisive factors in favour of performing the long-range ultrasonic testing for Chevron in Nigeria. As the inspection services of risers performed by SGS in early 2008 proved to be a great success, Chevron mobilised the SGS team to cover all the risers in the field, the process pipework as well as road crossings. SGS is now monitoring all critical pipework offshore, underground pipework as well as road crossings in the terminal.
www.sgs.com/ndt