Laser, video and ultrasonic inspection of pipe root welds is an oil and gas industry first
09/01/2012
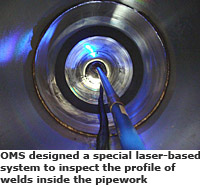
In late 2009, OMS was approached by a main contractor on an oilfield project and asked to provide a team of on-site inspectors to carry out a full inspection survey of a number of subsea modular valve manifold systems.
Using its laser-based dimensional measurement tools and video-based inspection systems, OMS was responsible for assessing the internal root welds for any defects. The inspection requirements covered the full range of weld features, including crown height, undercut, porosity and burn-through. OMS’s on-site inspectors were also required to perform inspections at welding temperatures (ie up to 250ºC). In order to do this, OMS adapted its own weld inspection technology to enable it to operate at these elevated temperatures.
Dr Richard Gooch, Director of Technology at OMS, commented: “On this project, the pipes on the modular valve manifold system were almost entirely lined with a special corrosion-resistant material. Our team of inspectors, therefore, had to make sure they didn’t overheat these coatings whilst carrying out inspections. On average, it was taking the customer around four days to complete a root weld pass. If there were flaws in a weld, this would have to be repaired or cut out. Our inspectors carried out their inspections immediately after the hot pass.”
“The laser and video-based inspection of root welds took approximately 10 minutes to complete. In this time, we gave our initial verdict to the customer’s QA engineer on whether we thought there was a problem with the root weld. If we were uncertain, the laser inspection procedure was repeated, but this time at finer detail (every 0.5 mm) than before, and double-checked using video-based inspection technology. The depth of the weld feature could then be examined more closely and a final verdict reached,” he added.
Whilst ultrasonic or radiography technology is commonly used to inspect pipe root welds, this technology is not so effective when the weld defects are very small, according to Richard Gooch. OMS provided a team of three inspectors at the site, one of these being a fully certified weld inspector.
“The modular valve manifolds are mounted on 30-foot skids and are critical junctions within oil or gas pipelines. Our inspection tools were able to pass around 90º and 33º bends in the pipework, as well as inside the valves themselves. In order to do this, OMS designed a special laser-based measurement system that incorporated a slide rail, stepper motor and optical laser sensor. This allowed us to push the tool in very small, half-millimetre steps through the pipes to inspect the profile of the welds,” explained Gooch.
OMS’s solution included blowing cold, compressed air over the inspection tool in order to combat the welding temperatures. A video camera was then used in combination with a shaft encoder to further inspect weld defect areas.
“This is the first time that these types of manifold systems have been inspected using a combination of laser, video and ultrasonic measurement techniques. The end customer asked for this and OMS was able to provide it. Many customers think that laser and video-based measurement techniques are too complex and so are only used in laboratory work and not in production environments, but OMS has proved the doubters wrong,” enthused Gooch.
www.omsmeasure.com