New drillstem component inspection certification
02/07/2007
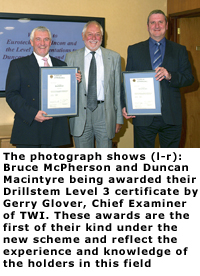
In an oil or gas well, the drillstem is the collective name for all the drilling tubulars extending from the drilling rig to the drill bit. A typical well may contain 400 pipes, each approximately 9 m long. Near the drill bit, and comprising roughly 10% of the total length of the drillstring, is the bottom hole assembly (BHA).
The BHA consists primarily of drill collars which provide the weight on the drill bit and is normally in compression. Above the BHA is the drill string, consisting of much thinner and more flexible drill pipe which extends upwards to the drilling rig and is normally in tension. Common to all components of the drillstem are rotary shouldered connections. These are coarse, tapered, male and female threads with a sealing shoulder, machined onto the ends of each component and which permit rapid addition or removal of individual components from the drillstem.
The stresses imposed on the drillstem during drilling operations can result in rapid accumulation of fatigue damage and frequent inspections are performed to detect mechanical damage and cracking in the rotary shouldered connections and in the tubes of drill pipe.
Typically, rotary shouldered connections are subjected to visual, dimensional and either magnetic particle or penetrant inspections. Drill pipe tubes are subjected to the same types of inspection as rotary shouldered connections, but additional inspections using ultrasonics (compression and shear wave) and electromagnetic (diverted flux) methods are performed.
Twenty years ago, the companies involved in the servicing of the drilling industry had very well-documented and formal internal training schemes. Inspection personnel were subject to formal, well-managed, training and certification. Now, however, the industry has changed and with it the formal training and certification. With very few exceptions, the service industry comprises small companies offering inspection/NDT personnel in a very competitive market.
The training and certification schemes, in general terms, do not formally address the specific requirements of the product, neither do they address the visual and dimensional controls called for in the relevant standards or specifications.
Thus, Eurotechnology studied their existing BINDT Approved training schemes with a view to bringing them up to date to meet the requirements of the standards and specifications currently being applied by the Industry.
Several meetings were held with representatives of the major oil companies, service sector, training establishments and certifying bodies.
The committee agreed that the remit was too extensive to have a 'one-fit-all' Training and Certification Scheme. The Scheme was split into the industry sectors:
Rotary Tool Connections or BHA (Bottom Hole Assembly) and Drillpipe
The two sectors were then sub-divided into the relevant inspection/NDT categories:
- Rotary Tool Inspectors
- Rotary Tool Inspector Supervisor
- Drill Pipe Inspector
- Drill Pipe Inspection Supervisor
- Magnetic Particle Inspection of Drillstem components
- Liquid Penetrant Inspection of Drillstem components
- Senior Drillstring Inspector (Level 3)
Once achieved then additional categories may be undertaken such as Drillpipe Inspector, incorporating ultrasonic methods for material evaluation, thickness measurement and manual end area inspection.
Whole-body electromagnetic (EMI buggy) inspection of drillpipe to incorporate magnetic flux leakage applications to be offered as a separate category as was the individual methods of magnetic particle inspection, liquid penetrant inspection and ultrasonic inspection.
All these training courses were to include general and specific theory together with specific practical application to drillstem components.
Eurotechnology-Incon has now been approved as an accredited training establishment for this course.
The examinations are independently processed by TWI Certification Ltd. This scheme now offers a uniform standard of competency throughout the industry.