SGS performs leak testing of heat exchanger for the first time
13/07/2010
In March this year, SGS Korea was assigned a contract to provide leak testing of a heat exchanger tube and tube-tube sheet in a refinery in Ulsan, Korea. SGS used this NDT method for the very first time on a heat exchanger.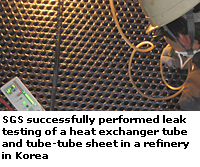
Due to SGS's extensive experience and competence in non-destructive testing, the leakage in the welding area of the heat exchanger was successfully identified and reported to the client. The successful completion of the project resulted in SGS receiving further contracts for NDT services from this client.
For the very first time, SGS applied leak testing, which had been limited to LNG carriers until now, to a completely new field. As leak testing of a heat exchanger tube and tube-tube sheet proved to be successful, SGS will expand its NDT technologies to new industrial fields.
In addition to leak testing of heat exchangers, SGS offers a heat exchanger life assessment system (HELAS), which is based on the measurement of ultrasonic immersion length, converted into the corrosion depth inside cooling water or air fin type tubes.
Thanks to SGS's global network and specific skills, SGS provides detailed data analysis and a complete lifetime assessment of heat exchangers by estimating the maximum corrosion with MVLUE (minimum variance linear unbiased estimate) and MLH (maximum likelihood) methods.
www.sgs.com/ndt