GE phased array drastically reduces pipeline inspection times
01/07/2011
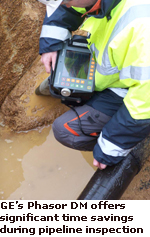
Stopple fitting is an important procedure in pipeline maintenance, carried out either to plug a pipe or to create a by-pass if flow cannot be interrupted. Before a stopple fitting is connected, the relevant area of pipe must be inspected for pipe compactness, pipe thickness and localised corrosion. Conventionally, this is carried out using a standard ultrasonic flaw detector and three sensors, one for each parameter. This is naturally time consuming and involves three separate calibrations for each sensor.
After witnessing a field demonstration of the Phasor DM for this application at Storengy, a subsidiary of GDF Suez, 2BTech decided to adopt the technique as a standard practice. As their General Manager, Philippe Becue, explains: “The Phasor DM has given us an enormous time advantage in these inspections, as we are effectively doing three jobs in one. This means that we can now inspect pipelines up to 200 mm in diameter in two minutes, as opposed to 15 minutes previously. For pipes above 500 mm, inspection used to take around 45 minutes. It now takes five to 10 minutes. Time is often vital in high-priority one-day excavations, as time saved in inspection allows more time for stopple fitting and backfilling.”
This Phasor DM thickness measuring, corrosion detection instrument features purpose-written software to optimise the potential of the specially developed multi-element phased array probe and the power of phased array imaging to display data in a meaningful and understandable way. The probe provides 28 adjacent and discrete elements to allow extensive linear coverage. The software then provides the ability to select and display the thickness measurement in each discrete beam, the minimum thickness in a current view and the minimum thickness recorded during a current scan since the last time the instrument was reset. It provides extensive linear coverage, so that an extensive area is inspected for thickness and wall density in every scan and even the smallest corrosion pit can be identified and measured. All data captured by the instrument can be downloaded by SD card in JPEG format as a B-scan for subsequent analysis, printing and archiving. The instrument’s onboard memory is sufficient to store the data of a meter scan.
“The Phasor DM also features integrated TOFD and SBA to allow a precise measuring option and, during an inspection, it is possible to modify a procedure and still be fully compliant,” adds Mr Becu. “Moreover, the new phased array technique has given us a distinctive commercial edge, as we are the first people in France using this.”
www.ge-mcs.com