Sperry Rail team gains honours for rolling contact fatigue system
10/06/2016
In January 2016, the Sperry Rail Surface Crack Inspection System team was presented with the ‘Track Technology Award’ at the UK Rail Industry Awards (UK RIA). This commendation followed the team’s acceptance of the ‘Innovation of the Year Award’, presented in September 2015 at the National Railway Awards. Both honours were in recognition of the latest innovations in track technology, whether for use on the track itself or alongside it, increasing efficiency, lifespan, safety or offering imaginative solutions to everyday tasks.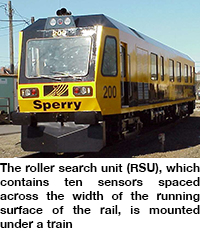
The Sperry Surface Crack Inspection System measures and reports rolling contact fatigue (RCF) using vehicle or pedestrian technologies. RCF is the generic industry term used to describe surface cracking on rails, which occurs in bodies in rolling contact. The Sperry Surface Crack Inspection System houses an eddy current roller search unit (RSU), which contains ten sensors spaced across the width of the running surface of the rail. The RSU is mounted under a train or in a pedestrian instrument and is pressed down to ensure contact with the rail surface. This system can be used in conjunction with ultrasonic testing methods and provides the following unique functions:
- Testing of the whole width of the running surface;
- Detection of both gauge and field-side RCF;
- Detection of centreline defects, such as squats;
- Accommodation of worn rail profiles;
- Testing of joints and misaligned welds;
- Testing of switches and crossings; and
- Testing at speeds of up to 35 mph.
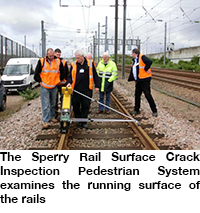
The project began four years ago with the aim of developing a system that would complement the non-destructive testing (NDT) that was currently in place for checking rails. The ultrasonic testing that was being used was ideal for inspecting volume, yet the addition of the Sperry Rail Surface Crack Inspection System allows the examination of the running surface of the rails. Bob Crocker, Innovations Group Inventor, said: “Increasingly, railways are using the results from NDT, not just for health and safety, but also to help make the most efficient use of their maintenance resources. The main thrust of most modern railways is that they are eager to develop their processes, to the point that there are no surprises. So, clearly, finding the crack at the earliest obvious point means that you can manage the defect and maintenance, as well as plan to complete the work at a very quiet time to minimise disruption.”
The Sperry Rail Surface Crack Inspection System team consists of: Bob Crocker, Innovations Group Inventor; James Crocker, Data Development Analyst; Justin Stroud, Director of European Business & Operations; Scott Saunders, Senior Development Engineer; Garry Pamment, Level 2 Eddy Current C/O System Assessor; and Damian Casson, Pedestrian Products Instructor. The team also worked closely with Professor Tony Peyton and his colleagues at the University of Manchester to build numerical models of rails and cracks to underpin the data coming from the field.
Network Rail provided on-going support throughout the prototype to production phases, in what has been a truly collaborative relationship, whilst exchanging vital information key to the product design, and has also purchased four vehicles. The vehicle system is currently operational in the UK, Ireland, Belgium, Switzerland and the USA, whilst the pedestrian instrument is on trial in these territories in addition to Germany, Sweden and the Netherlands.
“The team is extremely grateful to win both of these prestigious awards in recognition of the innovation that the Sperry Rail Surface Crack Inspection System offers and is continuing to gather essential information from the everyday use of the pedestrian and vehicle models,” concluded Bob Crocker.
www.bindt.org