B&K Vibro installs power station monitoring system in New Zealand
24/05/2019
Brüel & Kjær Vibro (B&K Vibro) has received an order for the supply of VC-8000 SETPOINT® systems and services for monitoring a 250 MW gas-/coal-fired steam turbine, generator and main boiler feed pump at Huntly Power Station, the largest in New Zealand. Huntly is owned by Genesis Energy, the third largest generating company in New Zealand in terms of production capacity.The B&K Vibro system provides both protection and condition monitoring of the generating units. In fact, the SETPOINT system represents the third generation of monitoring system from B&K Vibro installed at Huntly Power Station since 1995, following on from the Compass Classic and the VC-6000/Compass 6000.
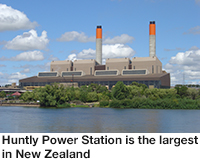
In addition to this, the VC-8000 is also able to stream all static and dynamic vibration data into the existing OSIsoft PI System data historian. Using the data historian server, this eliminates the need for a separate special-purpose vibration database.
This approach not only reduces IT infrastructure but also allows for easier correlation of process data with machinery vibration data, for advanced condition monitoring and diagnostics.
Once the data is in the PI System, it can be viewed using standard PI System visualisation tools as well as by B&K Vibro’s SETPOINT CMS software, which provides enhanced tools specifically for visualising and plotting vibration data. Core functionality within the PI System also allows customers to deploy advanced automated condition monitoring functionality and analytics that can continuously identify machinery problems and proactively notify plant personnel.