Neutron imaging: past, present and future
18/12/2019
In the aerospace sector, non-destructive testing (NDT) is vitally important. Aircraft and spacecraft have many components, such as turbine blades, ejection mechanisms, explosive signal transfer mechanisms and payload fairing separation mechanisms, for which the margins for failure are razor thin; new composite materials being developed for use in aircraft and spacecraft must be rigorously tested to ensure that they behave as expected in the research and development (R&D) phase. Any flaws in these components must be detected and eliminated early to mitigate the possibility of disastrous failures and accidents occurring. The aerospace sector has benefited heavily from one NDT method in particular: neutron imaging, also known as N-ray. Will Ascenzo, writer for nuclear technology company Phoenix LLC, based in Madison, Wisconsin, USA, explains…Neutron radiography was developed as a non-destructive testing (NDT) technique soon after the discovery of the neutron in the 1930s; however, it took until the 1950s for technology to develop to the point at which the technique yielded clear and detailed enough images for it to be useful in industrial NDT. N-ray functions similarly to X-ray, in that a beam of radiation is directed at an object and used to create an image of its internal structure, and the two are often used as complementary testing methods.
The difference between neutron radiation and X-rays, though, is that the rate of attenuation of neutrons does not increase with density in the same way as it does with X-rays. As a result, while X-rays easily pass through light materials and struggle to penetrate dense materials, such as bone or metal, neutron radiation passes through many of those same dense materials easily but struggles to penetrate lighter materials, such as water and plastic.
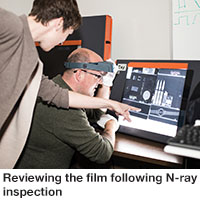
However, since N-ray facilities are scarce and can be difficult to access, most manufacturers in the industry do not have the opportunity to utilise N-ray for research and development (R&D), quality assurance or failure analysis and instead have to utilise other NDT techniques that may not be quite as well suited to the task at hand.
Neutron imaging is an immensely valuable inspection tool in quality assurance, prototyping and failure analysis of vital aircraft and spacecraft components.
Composites and additively manufactured components
By developing new composite materials, manufacturers in the aerospace industry can improve on existing designs and create components that may be lighter, stronger, more durable, more energy efficient or more environmentally friendly. For example, a composite material consisting of a durable material and a flexible material may possess attributes of both materials, augmenting each other’s strengths and shoring up their weaknesses. Composite materials can, for example, be used in the fuselage of a plane or in many other components to create an aircraft that is lighter and stronger and, therefore, faster and more fuel efficient.
Energetic materials
An energetic device is a device containing chemicals that, under the right situation, will explode with a carefully managed force. Energetic devices (ie explosives) play a pivotal role in the operation of aircraft and spacecraft. Painstakingly designed explosive charges that are meant to release just the right amount of force in just the right direction have little margin for error; if the explosive force is too strong or too weak, it can spell disaster.
When the pilot of a fighter jet needs to eject, a series of explosive charges separate the canopy from the rest of the aircraft and expel the pilot from the plane. Energetic devices also perform the critical role of separating the stages of a rocket as it ascends into space, a necessary process for shedding dead weight and releasing its payload. They are also used in explosive transfer line (ETL) systems, which function as basic signal transfer systems and are resilient against outside effects, such as high-radiation environments and electromagnetic pulses (EMPs), in a way that electronics would not be. In all of these mechanisms, if even one of these charges provides insufficient (or non-existent) force, then the results can be catastrophic.
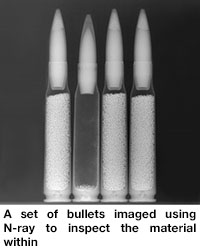
X-ray imaging tends not to work as well on these devices because very high-energy X-rays are needed to penetrate the dense metal exteriors; however, these same high-energy X-rays will pass right through the energetic material inside and be unable to provide information about the energetic material itself.
Neutron imaging, due to the unique properties of neutron radiation and its attenuation rates with various materials, is far better suited to determining the internal composition of these devices. As it turns out, neutrons are not only capable of penetrating the outer shells of energetic devices with ease, but also react strongly with the light chemical compounds within. Using neutrons, the shape of the materials within, pores, gaps, cracks and so on, may be seen clearly.
However, neutron imaging has seen little use by NDT professionals dealing with energetic devices due to the small pool of facilities that commercially offer N-ray as a service. Another reason why neutron imaging has seen such little use in dealing with energetic materials is because many of the facilities that do provide N-ray services do not have the capability to handle them, especially reactor facilities.
Since there are very few neutron imaging facilities in the world that can handle energetic devices, manufacturers often turn to X-ray CT to image them and remove materials with dangerous defects. Because CT scanning takes multiple 2D images of an object and compiles them into a 3D object, it can often reveal far more detail than a single 2D X-ray and can even show, with greater fidelity, the types of internal structure that a 2D X-ray would not pick up.
However, a single 2D N-ray image can reveal just as much data regarding the internal make-up of an energetic device as a 3D X-ray CT image. The same method used in X-ray CT scanning can also be utilised with N-ray to create a 3D neutron image. Overall, N-ray is a much easier tool to use for quality assurance and failure analysis than other methods of NDT.
Turbine blades
The manufacturers of turbine blades used in jet engines comprise the largest demographic of users of neutron imaging. This is especially true in the USA, where many of the world’s turbine blade manufacturers are headquartered. The specific issues that surround the manufacturing of turbine blades and the vital importance of rigorous inspection associated with these components underscore how powerful and valuable neutron imaging is as an inspection technique.
Turbine blades are cast in ceramic moulds out of strong, yet lightweight, metal that has a melting point lower than the operating temperature of the engine itself. If the blades are not properly cooled, they will melt and break apart due to the heat and stress. This is not good for the plane, its pilots and crew or its passengers.
Turbine blades require very rigorous quality assurance due to the high cost of failure. A single turbine blade breaking while in operation could cause engine failure and potentially lead to a plane crash and even loss of life. These blades operate in a very stressful environment; the tiniest overlooked flaw could spell disaster.
The solution turbine blade manufacturers settled on to prevent this scenario from occurring was the use of air cooling to keep the blades from growing hotter than their melting point. Airflow through the blades, facilitated by channels running through their internal structure, draws away heat and prevents the blades from failing while in operation.
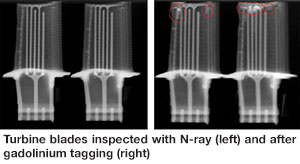
Neutron imaging is an effective and reliable NDT method for identifying blades with this type of flaw.
Neutron imaging works so well when inspecting turbine blades for ceramic remnants, due to one very special reason that relates to the unique properties of neutron radiation compared to X-rays. On its own, the contrast between the blade and the ceramic remnants is much greater than that shown by an X-ray image; however, neutrons alone may still have trouble showing all of the ceramic in a turbine blade, especially very small remnants. This is where another special feature of neutron radiation comes in: its high attenuation with gadolinium.
Gadolinium is one of a few elements that react very strongly to being pelted with neutrons. Due to its high neutron cross-section, gadolinium can be used as a powerful contrast agent in neutron imaging.
When the inside of a component such as a turbine blade is washed in a liquid gadolinium solution, the gadolinium will settle inside cracks, pores and other flaws. In particular, ceramic tends to be very porous (especially compared to metal), so it soaks up the gadolinium in a similar way to that of a sponge. This process of bathing a component in gadolinium is known as gadolinium tagging.
Imaging a gadolinium-tagged turbine blade yields stunning results. In a normal neutron image, the smallest remnants of ceramic within the blade remain unseen. However, with gadolinium tagging, the beam of neutron radiation passing through the blade will interact in a very different way with the ceramic bits that have absorbed the liquid gadolinium, making any flaws on the blade much more visible.
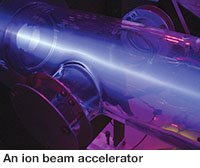
The vital importance of easy access to neutron imaging
In the case of critical aerospace systems, such as payload fairing separation, ejection and stage separation systems, the absence of neutron imaging facilities that are capable or willing to handle energetic materials means that manufacturers of these systems must use other means of NDT to ensure the quality of their products.
In the case of turbine blades, neutron imaging is a reliable way to detect certain critical and dangerous flaws. Turbine blade manufacturers have strong relationships with neutron imaging vendors. These relationships are so strong, in fact, that if a manufacturer loses access to its vendor, their ability to produce turbine blades and ship them out to customers grinds to a halt until the supply chain can be re-established.
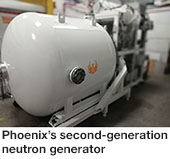
In Autumn 2019, Phoenix opened the Phoenix Neutron Imaging Center (PNIC), a first-of-its-kind radiography facility that, in addition to X-ray and CT imaging, offers both fast and thermal neutron imaging. Using Phoenix’s neutron generators, which have much lower regulatory burdens and a much smaller footprint than reactors, the facility can provide neutron imaging that is safer and more reliable than reactor facilities. PNIC is also capable of handling energetic materials. The facility will begin accepting orders from new customers in early 2020.
This facility represents a sea change in the world of neutron imaging. For now, PNIC is a one-of-a-kind radiography services provider. However, similar facilities can be built in the future across the world, greatly expanding the reach of N-ray and its usefulness as an NDT method in both the aerospace sector and many other industries.
www.phoenixwi.com