Eddyfi Technologies presents proven solution for in-ditch detection
01/02/2021
As industry faces catastrophic pipe rupture consequences from the presence of hard spots, it seeks new opportunities to ensure the continued safe operation of pipelines through early detection. Most hard spots are the result of unintentional quenching during a pipeline manufacturing process employed prior to 1970. Oil and gas pipelines constantly operate under cyclic stresses, which, combined with certain environmental conditions, may make them highly susceptible to cracking. The brittle and fragile nature of hard spots introduces an extremely dangerous vulnerability to pipelines, as any cracking that occurs in a hard spot will propagate significantly faster than anywhere else on a pipe. Hydrogen stress cracking accounts for the majority of failures associated with hard spots on in-service pipelines. Stress corrosion cracking (SCC) initiating in or around a hard spot can also create the perfect recipe for a pipe failure.In-line inspection (ILI) programmes are typically employed to detect metal loss in pipelines rather than report on hard spot anomalies, but can identify any suspect regions for further analysis during an integrity dig direct assessment. Nital etching is commonly used to validate any ILI calls. Given the intensive surface preparation required and the long process involved, the technique is only used in locations featuring indications, ie if a hard spot is not highlighted by an ILI tool, this integrity threat will remain undiscovered and reburied.
Acknowledging this challenge, Eddyfi Technologies has invested deeply in an inspection solution development programme in close collaboration with key pipeline owners and leading service providers. Recent laboratory and field trials have demonstrated the higher efficiency of eddy current array (ECA) over current techniques engaged for hard spot detection.
Eddyfi Technologies has introduced Spyne™, which it claims is the most efficient tool for hard spot detection on pipelines. Paired with Reddy®, a portable system offering 128 ECA channels, Spyne is preconfigured to deliver unprecedented scanning speed and coverage. An entire pipe surface can be examined in a substantially shorter amount of time, while ensuring any irregularities potentially not detected during the ILI are addressed. Accompanied by a high probability of detection (POD), the human factor is controlled with ease of use and repeatable data results on any detected hard spots. In addition to detecting hard spots, Spyne will highlight any linear indications found on the external pipe surface during an integrity dig direct assessment. These include SCC and hydrogen stress cracking, as well as fatigue cracks, lack of fusion and hook cracks in electric resistance welding, or manufacturing defects such as laminations and mill scabs. With the ability to accurately locate these pipeline integrity threats, operators can prioritise remedial action on the most critical regions.
Michael Sirois, Team Leader for pipeline direct assessment products, said: “After extensive trials both in lab and in-ditch environments, we are proud to say that the Spyne has set the new standard for hard spot detection on pipelines. As for the SCC, multiple tests were carried out on sample pipes as well as in-ditch, further proving the effectiveness of the tool. In a matter of minutes, compared to days for other methods, Spyne replaces the combined effort of nital etching and MPI for hard spot and crack detection, allowing decisions to be made more quickly.
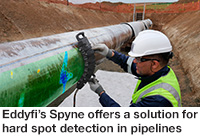
Eddyfi understands the implications of any missed pipeline integrity threats and offers the expertise to address specific requirements.
Eddyfi Technologies offers a diversified portfolio of NDT instruments, sensors, software and robotic solutions for the inspection of critical components and assets in key industries such as aerospace, oil & gas and power generation.