‘Into the deep’ with ACFM for swivel joint inspection
05/09/2016
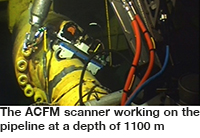
Swivel joints are an integral part of subsea pipelines and water injection systems, installed as part of the extraction infrastructure in subsea oil fields. Swivel and pipeline welds are made of a corrosion-resistant alloy, in order to avoid excessive corrosion. However, within the scope of TSC’s recent project, some of these joints had been identified as ‘leaking’, causing a reduction in the productivity of the well. Information and data on the exact nature of the failures were needed in order to schedule a repair and maintenance programme.
TSC’s ACFM® inspection technology has been developed to detect and size fatigue cracks in metal structures, with great accuracy, producing instant repeatable and auditable measurement data. The ACFM NDT method is tolerant of lift-off and misalignment and, as such, is suitable for deployment by ROV techniques in an underwater environment.
For this reason, ACFM was chosen and used to inspect the identified swivel joints to determine if there were fatigue defects present, as the detected leakage could be a result of cracking. ACFM was able to accurately size the known defects but was also deployed to determine if there was further cracking in the other swivels that could lead to failure in the short term. Automated ultrasonic testing provided by Sonomatic was also used to check the inside surface of the pipe for corrosion.
TSC’s ACFM equipment is rated for deepwater work, up to a depth of 2000 m. A scanner was designed and built in-house by the TSC engineering team, to work around the specified swivel joint geometry at the required depths. The scanning system also operated to cover the full circumferential weld of the pipe/swivel joints. The scanner maintains contact on the pipe using magnets and moves around the pipe guided by wheels that travel on the pipe surface. The ACFM probe is sprung to maintain contact with the weld being inspected and to minimise lift-off, for optimum sensitivity. As the ACFM inspection technique works through coatings, the epoxy surface preparation does not hinder the inspection.
Overall, this deep-sea inspection campaign was completed successfully and it was confirmed that no further fatigue cracks were present. However, there were corroded areas identified on the inner surface of the pipeline. Clamps were fitted to seal the leaking sections and to improve the productivity of the well. Further IRM activities are now being scheduled.
www.tscis.com