Successful Multicopters for Inspection Workshop highlights prospects and capabilities
26/09/2018
Drones have entered the public consciousness by producing dramatic new angles in numerous situations such as movies, nature programmes, sports events, concerts and weddings, etc. Drone racing, where the competitors wear a headset to create the impression that they are actually sitting on the drone while racing around a course, is becoming a sport in its own right. They are also being trialled as a means of delivering online products directly to your door. Unsurprisingly, their capability for producing images from a unique vantage point has made them attractive for carrying out inspections of assets that are normally difficult to access, or that require the costly erection of scaffolding in the case of a traditional inspection. Industry is awakening to the possibilities of this new technology, but is understandably a little unsure about how it is being regulated to produce a service that can be delivered safely while still having the necessary quality of deliverable.
The event was attended by about fifty people from industry, NDT service providers, training schools and universities, and was chaired by Colin Brett of Uniper Technologies Ltd. In addition, there were exhibits of drones from Inspectahire, Cyberhawk and the University of Strathclyde to give delegates a good idea of the types of drone and their capabilities.
A point of clarification is perhaps needed here: the term ‘drone’ can also apply to pilot-less underwater vessels. This workshop was aimed exclusively at aerial inspection systems using multicopters, so, rather than using this rather cumbersome term, we will continue to use the word drone.
Legal compliance, safety, operator accreditation and data protection are of paramount importance when carrying out any inspection, but it is perhaps more important for drone inspections than other types. No one wants a drone to fall out of the sky onto a switchyard and trip a plant, or even worse onto the operator or a member of the public. The first two presentations focused on these aspects and were given by Roy Amos of Panodrone Ltd and Adrian Wookey of the Engineering Construction Industries Training Board (ECITB). Roy explained the process for obtaining a Permit for Commercial Operations (PfCO), together with the regulations governing how high a drone can fly and, importantly, how close to people who are not directly under the control of the operator. He also gave information about other documentation such as insurance, flight log books, operations manuals, service records, etc, that any purchaser of an inspection service should demand and expect to see. Roy also highlighted the requirement not to acquire excessive footage that might contain information about individuals and their activities, in order to comply with the recent data protection regulations. The presentation from Adrian Wookey described how ECITB is developing a training programme that builds on the foundation provided by the PfCO to provide more specific training on the hazards and the precautions that are needed in the pharmaceutical, power generation, nuclear, oil & gas sectors. This is a rapidly evolving landscape and Adrian is happy to accept support from industry and training establishments to help make a robust accreditation system for operators.
The next three presentations highlighted the range of inspections that are currently being carried out using drones. Hugo Herrmann of EDF Energy R&D showcased two inspections being carried out on wind turbines. The first was to visually inspect the aerofoil surface of the blades for cracks and other features, avoiding the need for rope access technicians, and the second was to fly a caged drone inside the turbine tower to check for corrosion and other problems. The use of a drone means that the lower parts of a turbine do not need to be ventilated to remove toxic gases that accumulate in service, which would be the case if a human had to enter these parts. Inspections are therefore significantly quicker to perform.
Phil Buchan of Cyberhawk showed examples of drones in use to inspect a wide range of structures and components, including flare stacks and platform under-deck surveys in the oil industry, internal tank inspections, chimneys and cooling towers in the power sector, wind turbines and meteorological masts in the renewables sector and bridge masonry surveys. Thermal imaging is used for finding faulty components in electricity transmission towers and many other applications. Phil stressed the importance of providing data that can be used constructively by the client. To this end, Cyberhawk has developed software that can produce high-resolution three-dimensional models of the structure using the acquired images. This allows the client to home in on suspect areas and retrieve relevant data quickly.
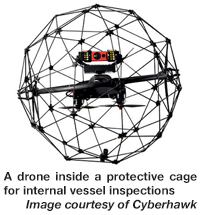
Tony Fong of the Offshore Renewable Energy Catapult then gave examples of images captured by drones that were not of sufficient quality to identify the faults that were hoped to be found. Insufficient resolution, over-exposure or a lack of focus can all degrade the images, resulting in a devalued inspection. The subjective judgement of the viewer is another factor, illustrated by the famous black and blue striped dress, or is it white and gold? Tony is about to start a round-robin exercise in which various companies will demonstrate the capabilities of their drones in inspecting an offshore wind turbine and identifying various known features. This work will help to develop image metrics and hence a standard for the cameras carried by drones. It will also cover the speed of inspection, the number of personnel needed and the overall reliability and repeatability. When completed, industry will be able to have increased confidence in the quality of any deliverables. It is hoped that the results of this exercise will be presented at a future event.
The last presentation of the day was by Gareth Pierce of the University of Strathclyde. He described work being undertaken to develop autonomous inspection systems, requiring no operator to pilot the drone. Pre-programmed flight paths are possible if there is a typical structure available as a reference. However, by using a laser mounted on the drone, it is possible to maintain a constant offset of the drone from the object being inspected without the need for a reference. Any images will then be well focused at all points. This opens up the possibility of being able to perform contact NDT using, for example, an ultrasonic wheel probe.
The final part of the workshop was a panel discussion in which the audience could ask the presenters any questions that had not been covered during the day, or to expand on previous answers. Of highest importance appeared to be the need for a robust accreditation scheme for the operators, and possibly the equipment maintenance personnel. Although individual companies have comprehensive in-house training schemes, it would be good to develop a standardised course so that purchasers of drone inspection services have confidence in the competence of individual pilots and the image assessors. The ECITB is working towards this and welcomes support from industry, drone companies and training establishments. Related to this is some form of international recognition for equivalent accreditations.
At present, drones primarily carry non-contact inspection systems such as optical and thermal imaging cameras, or LIDAR, but no contact systems. The audience asked if drones could carry ultrasonic or eddy current sensors that might be used to measure, for example, wall thicknesses or the quality of protective coatings at otherwise inaccessible locations. This is not possible now, but the work being carried out by the University of Strathclyde has shown that it might be feasible if drones can become more stable.
In summary, feedback from the participants has shown that the workshop was successful at delivering a range of information relating to the use of drones for inspection. The legal and safety aspects were outlined, together with the operator accreditation process, and many plant applications were shown that demonstrated the versatility of drones in inspecting locations that have hitherto been inaccessible without incurring large costs or endangering inspection personnel. This topic is changing rapidly so it is probable that the use of multicopters for inspection will feature at a future BINDT conference.
The presentations are available to view here.