Novosound enables efficient corrosion management programmes driven by real-time data
24/08/2021
Catastrophic safety failures and significant revenue losses can occur when corrosion goes unchecked. Recent figures report that corrosion costs production and manufacturing industries a staggering $17 billion (approximately £12.4 billion) per year. It is through energy losses, leakages and shutdowns for unplanned maintenance that these revenue losses occur, but currently it is difficult and costly to inspect every pipe and the supporting metal infrastructure for the progression of corrosion.Planning the most efficient maintenance regimes in tight schedules remains a challenge for plant owners and operators across the industry. Various solutions are available in the continuous corrosion monitoring market; however, there are several limitations regarding inaccessibility or the ability to operate within high-temperature atmospheres.
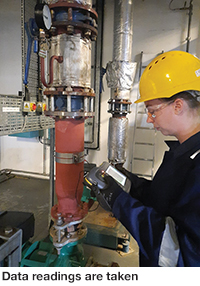
High-temperature corrosion (200°C+) in refineries can be attributed to the presence of non-electrolytes (usually gaseous H2S and H2), naphthenic acid corrosion, hot ash (fuel ash or salt deposit) corrosion and oxidation resulting from oxidation in furnaces. A number of refinery assets are particularly vulnerable to high-temperature corrosion, including distillation units, high-temperature process piping and decoking lines.
Within power plants, key pieces of equipment such as boilers are particularly susceptible to high-temperature corrosion. The upper section of a boiler, referred to as the penthouse area, is significantly affected by steam rising from the furnace below. These penthouse areas are subjected to extreme pressure and temperatures, resulting in a high incidence of corrosion. Power plant production processes necessitate using condensers, feedwater heaters and steam generators to derive, transform and transport water and steam throughout the facility and, again, this activity can produce harmful effects on the metal and pipework structures.
The Novosound Belenus is a simple, smart ultrasound sensor enabling 24/7 monitoring of the corrosion and erosion of pipework in these most difficult, challenging and safety-critical environments. It utilises ultrasonic pulse-echo to monitor pipe wall thickness: an ultrasonic signal is generated in the pipe and the time taken for a reflection to be detected allows for the calculation and visual display on a data acquisition unit of the pipe wall thickness, with a faster arrival time indicating that the pipe wall is thinning.
The Belenus is manufactured using a highly flexible thin-film material. This allows for a simple compression fitting installation to any component shape, including small access areas and challenging geometries using just one type of sensor. The flexibility also permits coupling without the need for a gel or oil-based couplant, which evaporate at high temperatures. Combining its compact size (50 mm × 32 mm × 20 mm) and flexibility, the Belenus can be easily fitted to challenging branches and pipe elbow bends, which are often considered the weakest part of a pipeline system and are therefore recognised as one of the most critical parts in terms of failure.
For example, subject to heat cycling conditions, chemical corrosion and long service times, riser tube bends are vulnerable to significant corrosion fatigue damage. Corrosion can cause pinhole leaks in the riser tubes and subsequent damage to adjacent tubing and boiler parts. Riser tubes can eventually rupture, posing a major safety threat and leading to unplanned interruptions and shutdowns.
The novel utilisation of ultrasonic thin-film material means that the Belenus has no intrinsic Curie temperature, unlike most standard sensors. It is claimed that this makes it the world’s first corrosion monitoring sensor that can operate completely soaked in high-temperature atmospheres up to 400°C for extended periods of time without the need for welding, coolant, couplant or delay lines.
In contrast, conventional piezoelectric materials used in ultrasonic sensors lose efficiency and acoustic output when exposed to increased temperatures due to their Curie temperature limiting their effectiveness for continuous monitoring at elevated temperatures. This means that current ultrasound sensors require delay lines or a limited exposure time to ensure they are kept at lower temperatures, resulting in a poor signal and reduced performance.
With the ability to continuously operate at high temperatures up to 400°C, the Belenus allows corrosion to be detected in pipes without the shutdown or cooling of assets, therefore greatly reducing maintenance costs and downtime. This also enhances safety as it limits staff exposure to high temperatures and hazardous environments. Additionally, without the need for a delay line when operating at high temperatures, there is no loss of signal between the sensor face and asset, therefore providing more accurate measurements.
Conventional ultrasound sensors are traditionally manufactured using machining and other manual processes, whereas thin-film sensor production is an additive process capable of coating large areas of substrate for assembly into multiple devices. Manufactured in its entirety in Novosound’s West of Scotland facility, the additive process of thin-film manufacturing makes Belenus sensor production highly scalable and cost-effective, therefore making the monitoring of large assets viable.
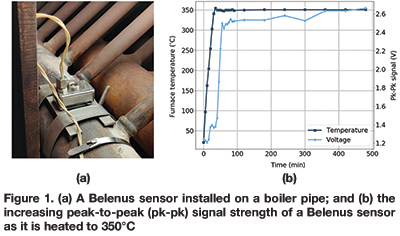
When completing the installation, there was restricted access to the burner and tight working spaces. The entire sensor housing is 50 mm long, less than the size of a matchbox, meaning it is suitable for tight spaces. This can be seen in Figure 1(a), where the Belenus has very limited space around the inspection pipe. Its compact size facilitates a quick and simple installation, with minimal interruptions to plant operations and no subsequent effect on the structural integrity of the asset. As a result, the client now has access to thickness measurements at all times as opposed to only being able to take manual readings at defined shutdowns. Figure 1(b) shows how the signal strength of the sensor doubles when heated to 350°C, whereas a conventional sensor displays a weaker signal over time.
Via Novosound’s cloud-based system, the Nebula, plant operators can access inspection data remotely at any time. At the heart of the system is a powerful datalogger that will interrogate sensors and capture data. This data is stored, processed and managed in the cloud through the use of secure protocols. This allows for key operational decisions and analysis of the integrity and condition of assets across a range of locations via the optimal data transfer protocol, whether wireless or cabled.
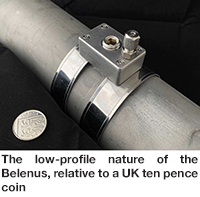
www.novosound.net