Special sensor makes modern aircraft fuselage assembly safer
17/02/2011
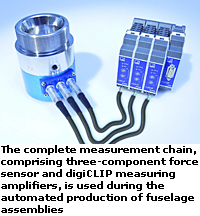
These modern innovative composite materials are increasingly being used in aircraft construction and pose new challenges for manufacturers trying to optimise manufacturing costs and runtimes while ensuring the materials are used safely.
HBM has combined the three-component TEDS (transducer electronic datasheets) sensors with its ‘digiCLIP’ modular measuring amplifier system. This enables HBM to provide a complete measurement technology solution that establishes a new milestone for economic efficiency and effectiveness, both during installation and on-going operation.
The specially developed three-component force sensors are used to check forces on the fuselage sections during assembly. Signals from the force sensors are acquired by the digiCLIP measuring amplifiers and transmitted to the plant control system. A large number of measurement channels can be easily set up by mounting on DIN rails and daisy-chain wiring to meet the size and complexity of any assembly line.
A characteristic feature of the digiCLIP amplifiers is their noise-free and stable measurement technology, which ensures reliable measurement results in industrial environments. The amplifiers are integrated into the automation architecture via the Profibus DP interface.
The modules have an internal digital signal processor that calculates process-relevant quantities during the assembly process, such as instantaneous values, peak values of the press forces and limit value violations.
HBM constantly researches and supports new automated assembly concepts with innovative solutions, such as the three-component TEDS sensors with digiCLIP modular measuring amplifier system, for process monitoring.
www.hbm.com