Ultrasonic Sciences celebrates record year
01/03/2013

In the first few weeks of 2013, the installation and commissioning of these systems was nearing completion, whilst at the same time USL’s largest ever squirter inspection system was delivered to Japan. This machine, with a scan volume of 14 × 1.8 × 2.9 m, will be used by a manufacturer of aerospace composites for the inspection of parts being manufactured
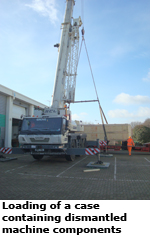
Packing and shipping a system of this size poses some significant logistical problems. In this case, the consignment totalled 33 tonnes and required eight custom-made packing cases, three large articulated trucks and the same number of transport aircraft. The pictures show just one of the cases being loaded and the truck convoy leaving the USL factory.
A further four similar, although smaller, systems are currently under construction, together with several immersion testing units of various sizes.
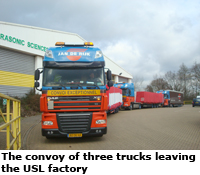
www.ultrasonic-sciences.co.uk