Improving Productivity with Lubricant Analysis
26 November 2024
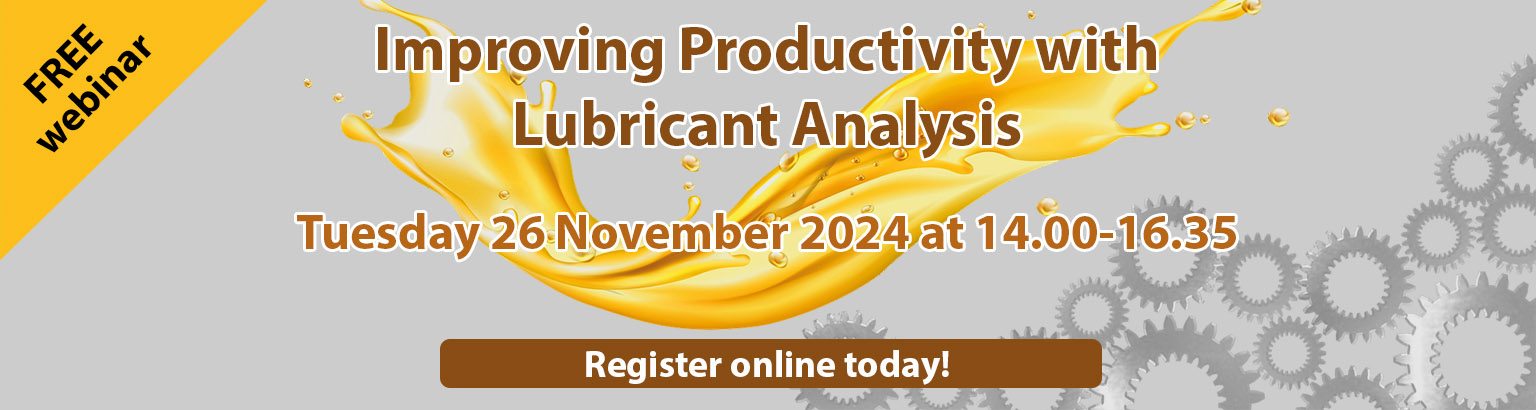
The common definition of ‘productivity’ is the rate at which a worker, a company or a country produces goods and the amount produced, compared with how much time, work and money is needed to produce them. In short, increasing productivity means doing more for less. When it comes to lubricant analysis and lubrication itself, we benefit by doing this right and by being efficient we can achieve a much better return on our analysis investment.
This webinar was curated to highlight improvements through accuracy, oil life extension, early wear detection and contamination management. In addition, we looked at maintenance forensics where we align lubricant analysis outcomes to optimisation of the maintenance activity, and the merits of condition-based lubrication to only apply lubricants when needed and to ensure that the right amount is applied every time.
Lubrication, and its management, is considered to be one of the most important activities any industrial plant needs to perform well, yet there are many examples of where this is not given the attention that it deserves and where, unknowingly, productivity gains are not being achieved. In this webinar we will target several approaches that are known to lead to real and meaningful gains.
Programme | |||
14.00-14.05 | Welcome and introductions | Danny Shorten John Crane Asset Management Solutions, UK | |
14.05-14.25 | Improving productivity through more accurate analysis techniques Oil condition monitoring (OCM) is a branch of the science of condition monitoring (CM). All science domains are founded on fundamental dimensions of mass, length and time. There are methods carried out by OCM, where these rules do not apply. This limits the value of the results obtained and possibly hinders industrial productivity. The presentation intends to highlight this issue and show how two such methods have been resolved. | Robert Cutler Oil Analysis Laboratories, UK | |
14.25-14.45 | Online oil quality sensors. Case study of lubricant life extension without risk of missed failures or secondary damage from aged lubricants With ever-increasing cost controls, as profit margins are squeezed by market pricing, and the recent advances and enhanced capability of online sensor technologies. There are now several reliable and robust oil quality sensors available in the condition monitoring marketplace. These sensors are enabling oil quality assessments to be made remotely, 24 hours a day for a one-off fee. This paper outlines, through an actual case study, a sensor combined with the skills of trained CM staff and demonstrates how the advantages of both lubricant life extension and machine oil health monitoring may be combined in a cost-effective manner. | Steve Greenfield Anokhi Consulting Engineers, UK | |
14.45-15.05 | Early detection of incipient wear within oil-wetted systems Wear debris is generated within all rotating systems. Sampling and analysis of wear debris from an oil system can give a good indication of the health of assets, with composition, size and shape of the wear debris all being used to provide an assessment on the condition of systems. By gaining a valuable picture on the condition of systems, it allows any potential concerns to be addressed before they develop into costly problems. | Tim Nowell Intertek Fuels & Lubricants Centre, UK | |
15.05-15.15 | Comfort break | ||
15.15-15.35 | Diagnosing lubricant contaminants, quantifying effects on productivity Did you know that with an ISO code of 22/21/18 your asset could be circulating roughly 4+ tons of debris per year? What does that mean for your productivity? Water, debris, wear debris, air – it all takes its toll on our assets and site reliability, but what does that look like for productivity? Understanding the contaminant, quantity and cause will help you pinpoint an optimal solution. Quantifying the cost to productivity will help you justify the solution. | Jade Thompson SKF (UK) Ltd | |
15.35-15.55 | A quick guide to maintenance forensics Understanding the mechanisms of degradation and failure are vital to improving reliability. Just as in criminal investigations, ‘forensic’ tools can be applied to understand the causes of failure and identify the origins of external contaminants. This presentation will describe some of the available instruments and techniques as well as the practicalities of engaging a laboratory partner to assist with the investigation. | Dzmitry Korachkin Swansea Tribology Services, UK | |
15.55-16.15 | The merits of condition-based lubrication Oil sumps and hydraulic reservoirs, etc, have bulk volume that circulates and can be assessed using level gauges or site glasses. These simple devices provide feedback to our technicians, which can then be used to trigger a top-up to ensure the quantity of oil is optimal for each asset. But what about greasing bearings either on motors or systems where there are multiple grease points? Some systems such as single-point auto lubes can be used or multi-point single- or dual-line progressive fitted. However, how can we ever know whether we are adding the right amount and at the right frequency? This presentation will cover the basics of calculating volumes and frequencies and how we can use technology to gain feedback that lubrication is being controlled and know when each bearing has been optimally lubricated. | Danny Shorten John Crane Asset Management Solutions, UK | |
16.15-16.35 | Panel session with Q&A |
Organised by the BINDT Lubrication Analysis Working Group.
For further information, contact:
Events and Awards Department, Midsummer House, Riverside Way, Bedford Road, Northampton NN1 5NX, UK.
Tel: +44 (0)1604 438300; Email: conf@bindt.org