Ultrasound Technology
What it is ...
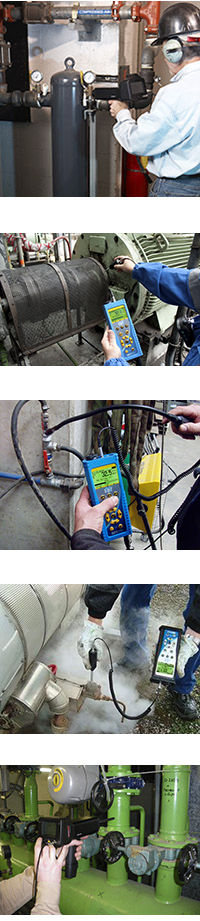
Ultrasound is inaudible. Traditionally, ultrasound systems use heterodyning or mixing techniques to present a signal to a headset that would typically have audible frequencies in a range around 2 kHz. Once you get past the ‘cheap and cheerful’ systems, which merely click or whirr to represent the presence of an ultrasound signal, to one which uses this mixer technology, you have a system that actually allows the user to listen in on what is going on far beyond the natural range of hearing. In fact, some instruments on the market allow operators to change the mixer frequency so that they can listen to frequencies up to almost 200 kHz. This is fascinating when you think about it: you can actually listen in on what is happening far beyond the capability of your ears. If there is a click, knock, rattle, whirr or hiss at 40 kHz, that’s just what you hear when you set your instrument to be within 2 kHz of that frequency.
Measuring ultrasound
Ultrasound is treated, quite rightly, as a sound, which means that when quantifying the level of ultrasound signal we are listening to we use a decibel scale. Unfortunately, the arrival of the electronic calculator in the 1970s meant that complex arithmetic could be performed without the aid of log tables and so very few people understand decibels anymore. Log tables helped in all manner of engineering feats. Two key features of this relatively simple arithmetic are that:
- Any number can be represented as a power of 10. We all know that 10,000 = 104 for example. The log of 10,000 is 4. The log of 20,000 would be 4.3.
- When we want to multiply two numbers together, we add their logs. When we want to divide, we subtract their logs.
- dBs are never multiplied or divided.
- The dB is a logarithmic ratio scale and you cannot have a ratio without a reference value.
- In itself it is not a unit of measurement; the measurement unit is the bit on the end: dB(A), dBm, dBV or dBµV could be termed units of measurement.
Ultrasound example applications
Applications for ultrasound technologies are widespread and include, but are not limited to, the following application areas:
- On-condition lubrication
- Rotating machinery
- Valves
- Compressed gases and vacuum leaks
- Steam leaks and steam traps
- Hydraulics
- Electrical
- Tightness.
Ultrasound education & certification
The use of ultrasound technology in condition monitoring is one of the key activities in predictive maintenance programmes for most industries. Those in the manufacturing industry who have diligently and consistently applied these technologies have experienced a return on investment far exceeding their expectations. However, the effectiveness of these programmes depends on the capabilities of individuals who perform the measurements and analyse the data. ISO 18436 defines the requirements for personnel to become qualified to apply the non-intrusive machine condition monitoring and diagnostics technology of ultrasound.
The full title of this standard is ISO 18436-8:2013, ‘Condition monitoring and diagnostics of machines – Requirements for qualification and assessment of personnel – Part 8: Ultrasound’.
A programme, administered by an assessment body (such as BINDT), has been developed to train and assess the competence of personnel whose duties require the appropriate theoretical and practical knowledge of machinery condition monitoring and diagnostics.
ISO 18436 defines the requirements against which personnel in the non-intrusive machinery condition monitoring and diagnostics technologies associated with ultrasound for machinery condition monitoring are qualified and the methods of assessing such personnel.